
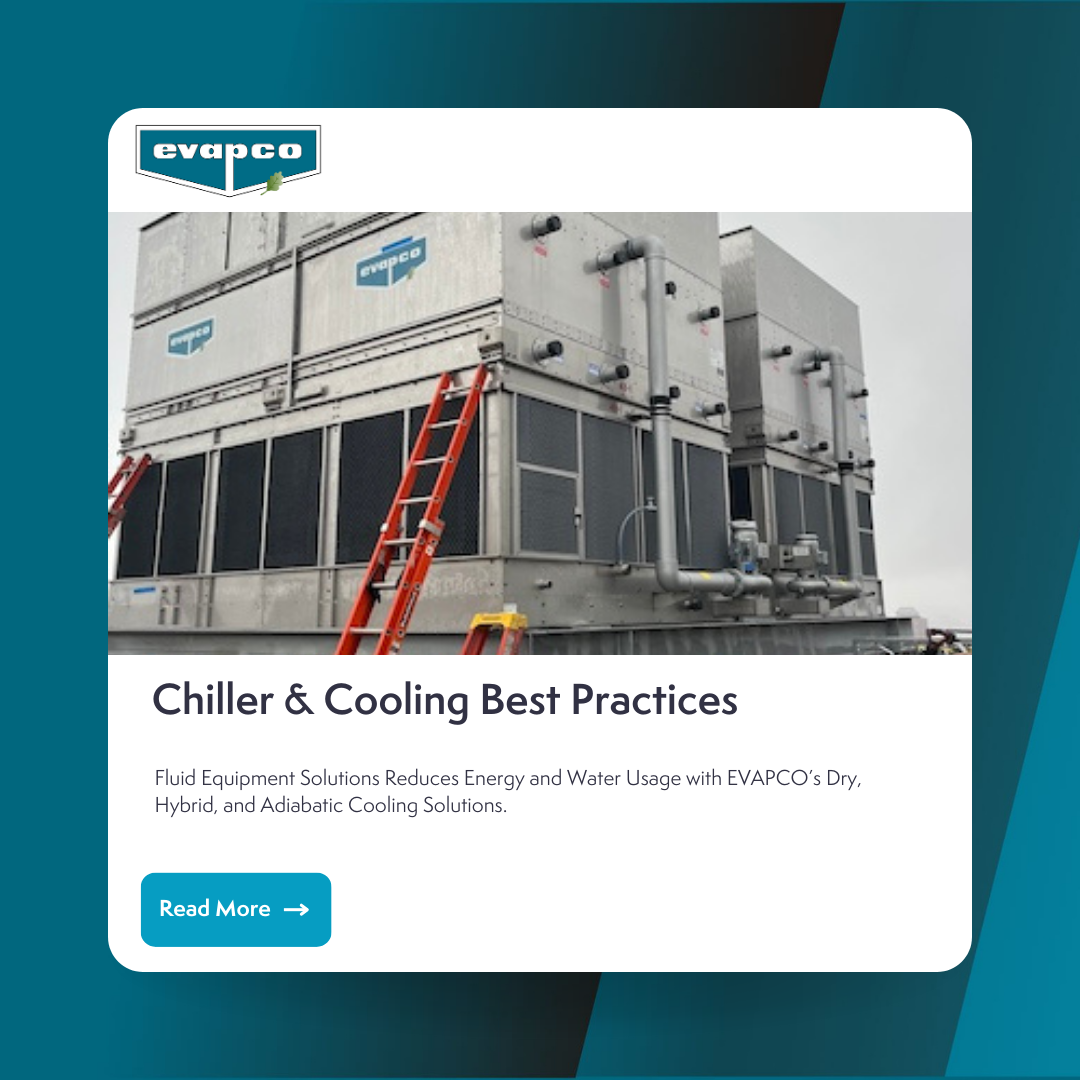
FES is involved in the full lifecycle of its projects. Its sister company under the same ownership, Good Tower Services of New England, handles all startup, warranty and field service work. A sale to a mechanical contractor typically involves a startup in the field. McLaughlin likes to tell the lead service technician doing most of the startups that he’s an important part of the organization because he puts a bow on the project.
“As a rep firm, we are a unique presence in our industry. We’re involved in the lifecycle of our cooling towers and fluid coolers before they exist all the way to the end of life. We’re even involved in service and maintenance in partnership with our contractor customers,” McLaughlin said. “That's unique. We work with a consulting engineer on the design, we bid the product and, hopefully, work with the mechanical contractor and sell it to them. Then, Good Tower Services, our parts and services arm, works hand-in-hand with the installing contractor on startup and commissioning.
“We’re often called upon by our mechanical contractor customers, as well as owners, asking, ‘How can we extend the life of this product?’ We’re careful to work with our contractor and owner customers to find solutions,” McLaughlin said.
Another thing distinguishing FES is the limited size of its product offerings. Because the company keeps its product offerings small, it’s able to have a high degree of expertise. McLaughlin noted the company is consistently one of the top-performing EVAPCO reps in the country.
“We maintain high product and application knowledge, and that allows us to give a high level of personal service,” McLaughlin said.