
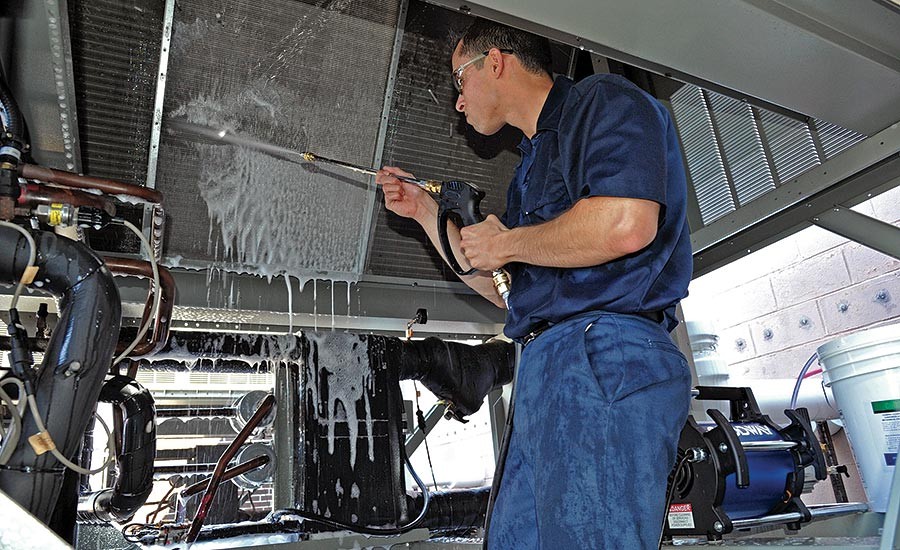
A coil-cleaning program should be an integral part of maintaining some kinds of process cooling equipment.
Most people think of coil cleaning as a building or facility prepares to turn on the air-conditioners for another season. Admittedly, spring is a perfect time to put such cleaning and maintenance at the top of the to-do list. Condenser and evaporator coils are an integral part of HVAC systems, and one of the quickest and safest ways to maintain them is through a comprehensive coil-cleaning program. Even the best, most expensive system will not reach its optimum performance without proper maintenance, and a building’s heating and cooling systems account for 60 to 70 percent of its total energy use.
But, HVAC systems are not the only cooling coils that benefit from regular maintenance. Process cooling equipment like blast chillers and refrigeration equipment greatly benefit from scheduled maintenance to maintain peak efficiency. It is certainly not an area to cut corners.
Rising energy costs and the accumulation of dust and debris in the coils or ducts are two indications that it is time to clean your system. It also is important to keep the process equipment clean and free of any contaminants or potential hazards for safety and health reasons. You do not need to wait until red flags like rising energy costs to appear, however. You can be proactive and address the concerns before they become an issue to ensure a clean and safe processing or manufacturing environment.
The Impact of Deferring Maintenance
Postponing maintenance and cleaning can have a detrimental impact on process equipment and heating and cooling systems. When dirt and grime coat a chiller’s or air-conditioner’s coils, it can drastically increase the costs of running that system. For instance, the average annual cost of dirty coils for a 100-ton HVAC system is $22,500. Studies have shown that there can be up to 16 percent in efficiency gains simply from coil cleaning on a routine schedule. Dirty coils likewise affect critical equipment such as chillers, cooling towers and boilers. If equipment is running harder than it should be because of dirty coils, the undue strain on the system components can lead to costly damage or necessary repairs.
Perhaps even worse, dangerous bacteria can multiply in poorly maintained systems or equipment, posing health risks such as asthma, nausea and more for a facility’s occupants. The evaporator coil and its condensate pan can become fouled with pollen, mold spores and other biocontaminants. These can have an adverse effect on indoor air quality and even spread to manufactured items. With all the moisture around the evaporator coil, it can become a breeding ground for bacteria and mold.
Overall, the benefits of clean coils include energy savings, maximum heat transfer, system longevity and improved air quality.
Coil-Cleaning Equipment and Chemicals
Plenty of tools only require simple training. Advancements in technology and design have helped to make coil cleaning easier and less time-consuming. The equipment lends itself to increased portability for smaller spaces.
It is important to make sure you are investing in the right equipment for your maintenance needs. Take the time to speak with the manufacturers of the products you are researching. They can suggest features that will make coil cleaning easier and more effective.
Look for a coil-cleaning system that uses an appropriate amount of water pressure to remove the dust and debris from evaporator and condenser coils. While pressure washers are one of the more common methods, they can do more harm than good if their excessive pressure damages the coil’s delicate fins.
When cleaning indoor coils, use tools designed for minimal yet sufficient pressure. Limiting the amount of water and chemical used will ensure you do not overwhelm condensate lines. On outdoor coils, use a combination of lower pressure and high water volume to thoroughly clean coils.
Finding the right coil-cleaning chemical is just as important. Acid cleaners are unsafe for workers, destructive to coils and other components, and not environmentally friendly. A biodegradable, alkaline coil cleaner with a foaming component is an alternative. Also, EPA-registered mold and mildew inhibitors that contain any growth and improve indoor air quality can be used to treat indoor coils after cleaning.
Coil-Cleaning Checklists
The following steps are recommended when performing coil cleaning.
Cleaning Air-Handler Coils
- Be sure the system is shut down.
- Locate the air handler and make sure there is proper access to get close to the coils.
- Eliminate any dry debris by using a vacuum to clean coils and fins.
- Be sure the condensate pan and lines are free from blockage before you begin cleaning.
- High pressure cleaning equipment can damage delicate fins, and high flow units can overwhelm drain pans. Consider a coil-cleaning system that delivers around 125 psi and 0.5 gal/min.
- Apply noncaustic, nonfuming coil-cleaning chemicals and let them sit for a few minutes to penetrate. Pay close attention to the instructions on the coil cleaner.
- Thoroughly rinse off the chemical and repeat the cleaning if necessary.
- Treat coil and plenum with an EPA-registered mold inhibitor to prevent bacterial and mold growth.
- Clean the condensate pan and drain line. Use drain pan biocide tablets to minimize the risk of future blockage and flooding.
- Restart the system and get back to business.
Cleaning Condenser Coils
- Be sure the system is shut down.
- Make sure there is access to water and power to use with the coil- cleaning system.
- Avoid high pressure cleaning systems that can damage fins. Consider a cleaning system that produces 400 psi at around 3 gal/min in order to flush out dirt and debris.
- Apply noncaustic, nonfuming coil- cleaning chemicals and let them sit for a few minutes to penetrate. Pay close attention to the instructions on the coil cleaner.
- Flush coils with water, working opposite the airflow to push dirt out the way it came in.
- Power the unit back up.
Enforce the Maintenance Plan
Spending a little on regular maintenance will save a lot on repairs and extend the life of the equipment in the long run. First, make sure the facility has a plan that builds in time for critical process equipment maintenance at least annually, if not twice a year, between heavy-use seasons. Having a maintenance plan in place — and sticking to it — helps prevent unexpected and costly breakdowns, outages and repairs. Second, an under-utilized tool in the plant maintenance toolkit is an operating log. These logs help track information related to the system’s operation. Facility managers can see when maintenance or repairs may be needed or when readings outside the norm occur. Operating logs also are helpful to track trends, measure improvements and compare data year-over-year.
Measurement is an often overlooked or skipped task because it takes extra time. It can be hard to figure out what and how to measure if there is no plan in place. In fact, one survey by a coil-cleaning equipment company showed that only 39 percent of the respondents measure the efficiency gains resulting from chiller cleaning. You cannot effectively manage what you do not measure.
Coils in process and HVAC systems make up some of the plant’s largest operational expenses. Measuring the gains in energy efficiency as a result of regular maintenance shows the impact of the facility managers’ work in a way that is meaningful to upper management: cost savings.
Original article found here.